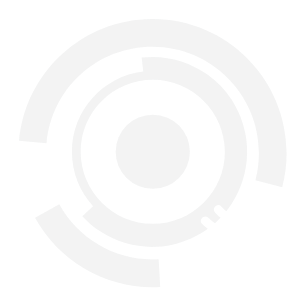
Richiesta Informazioni
Contatta direttamente LAB.MET. S.r.l.
- Catalogo
- Listino prezzi
- Lista rivenditori
- Contatta agente
Compila il form (I campi indicati con * sono obbligatori)
Dichiaro di aver letto ed esprimo il mio consenso al trattamento dei dati per le finalità dall'informativa privacy.
Rete d'impresa e contatti di settore
Servizio di connessione diretta alle aziende di interesse nell'indotto. Proponiamo un implemento del business model attraverso nuovi contatti nel settore.
Scouting fornitori
Ricerca di nuovi partner sulla base delle necessità del cliente.
Portale web dedicato
Una vetrina esclusiva dei prodotti nel mondo Oil&Gas. Un ampio catalogo web di aziende appartenenti a questa realtà suddivise per categoria.
Catalogo come strumento di selezione e visibilità
Un catalogo cartaceo come strumento di ricerca di nuovi partner. Un'esperienza tangibile che rende concreta l'idea della fiera virtuale.
Marketing Digitale e Comunicazione
Servizio di comunicazione e web marketing settorializzata nel mondo Oil&Gas ideato per coprire a 360 gradi la brand identity di ogni cliente. Dallo studio del logo alle strategie di immagine e follow up di social media.
EVENTI
Grazie agli ottimi risultati raggiunti, abbiamo deciso di organizzare i primi eventi Expo Valve. Ai nostri eventi potranno partecipare esclusivamente i nostri clienti. Saranno ospiti e relatori alcuni tra i leader del settore, giornalisti e personaggi pubblici. Abbiamo in programma la discussione di temi attuali e d’interesse per tutti i nostri partner. Attraverso queste occasione di incontro, sarà inoltre possibile creare nuovi contatti e potenziali collaborazioni tra espositori Expo Valve.